LES GRANDES ÉTAPES DE LA FABRICATION DE L'ACIER
A cette époque, la fabrication ancienne est remplacée, le procédé est dit indirect. Les bas-foyers sont remplacés par les hauts-fourneaux, la soufflerie est mécanique et on passe de la loupe de fer à la fonte.
Extraction du minerai de fer
A Poissons, il était extrait à partir de couches quelques fois à trente mètres de la surface, au moyen de pics, remonté à dos d'homme sur des échelles attachées en doubles ou triples, et dans des paniers ou bien au moyen de treuils ; ce qui n'était pas sans danger. Tout le monde connaît à Melaire l'existence de ces trous, dont certains ne sont ni connus, ni accessibles. Des attelages descendaient ces chargements vers les patouillets.
Le lavage (patouillets)
Après avoir longtemps lavé le minerai à la force des bras, la mécanisation (hydraulique) apporta la rentabilité et la réduction de travaux pénibles. Les traces rouge-argile témoignent, le long de la rivière, des endroits où étaient installées ces machines : Chenesonval, et aux Noues.
Le concassage (bocards)
Au moyen de bocards on réduisaient le minerai à une taille correcte pour qu'il puisse être fondu. Ces bocards servaient également à concasser des crasses pour le remblaiement des chemins et routes, et se situaient en aval des installations.
|
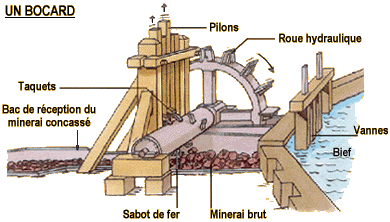 |
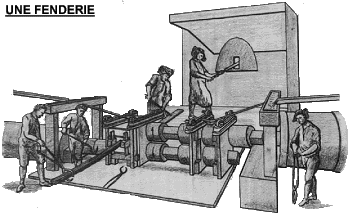 |
Dans le Haut-Fourneau (H-F)
Il fallait alterner couches de minerai, couches de charbon de bois dans une grosse cornue, allumer le charbon et forcer la combustion au moyen de soufflets mécaniques pour faire fondre le minerai qui finissait par couler au bas de l'édifice sous l'appellation de fonte. En 1785 la France utilise le coke (extrait de la houille) en remplacement du charbon de bois qui restera le seul combustible en Haute-Marne jusqu'en 1845.
|
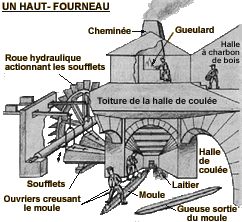 |
Transformation de la fonte en fer.
La méthode comtoise consistait à réchauffer dans l'affinerie, la gueuse sortie du H-F (poids de la gueuse : une tonne et demie environ pour une longueur de deux mètres) et la diviser au moyen d'un pic appelé fourgon, pour en rassembler ensuite une partie sur le refouloir, la masse était toujours à haute température ; le poids correspondait alors à la pièce à fabriquer ; cette masse appelée "renard" (structure poreuse) était progressivement débarrassée du carbone (par l'oxygène de l'air soufflé) qu'elle contenait, et fortement cinglée par le marteau de 250 kg (hydraulique) qui reconstituait par les chocs et affinait une barre de forme marchande. La barre sous cette forme, sera employée comme telle ou vendue à d'autres affineurs plus spécifiques.
|
La première difficulté étant de faire passer la gueuse du haut-fourneau vers l'affinerie ; les deux bâtiments étaient proches. A La Forge, passait-elle au dessus du bief...? Alors commençait dans le foyer d'affinage, avec l'élévation de température, la mise en morceaux puis la constitution d'une masse spongieuse afin d'en faire un produit marchand. Le cinglage avec le marteau faisant partir le laitier (crasses et autres impuretés) étirait la barre de métal. Elle était réchauffée et martelée souvent plusieurs fois, en fonction de la taille définitive. Pour de plus petites sections de barres le martinet ne pesait qu'une centaine de kg, pour encore plus petit, genre fils de fer, la fenderie était équipée en tréfilerie. |
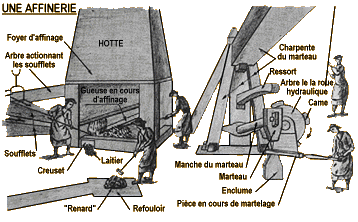 |
La méthode anglaise, utilisait du coke dans le H-F, avec un four à puddler (chauffé à la houille) et une fenderie équipée d'une série de laminoirs, elle n'a été employée que vers 1825 à cause du coût de l'investissement. La forge de Doulaincourt était équipée à l'anglaise.
La méthode mixte appelée champenoise utilisait un four à puddler pour la transformation mais pouvait garder son équipement existant dans l'affinerie moyennant seulement quelques modifications.
|
|